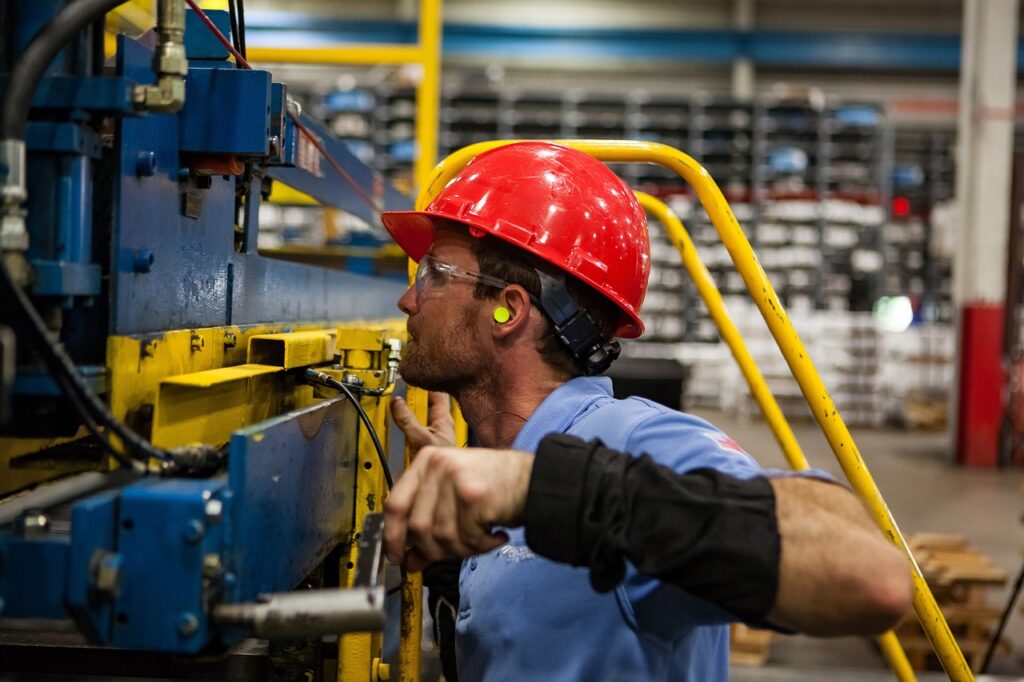
Introduction
The manufacturing industry is undergoing a significant transformation driven by the adoption of advanced technologies. Among these innovations, chatbots stand out for their ability to streamline operations, enhance productivity, and improve overall efficiency. As factories embrace digital transformation, chatbots are playing an increasingly vital role in revolutionizing the manufacturing landscape. This blog delves into how chatbots are reshaping the industry, offering insights into their applications and benefits.
The Rise of Chatbots in Manufacturing
Chatbots, powered by artificial intelligence (AI) and machine learning, have become invaluable tools across various industries. In manufacturing, they are being deployed to handle a range of tasks, from customer service and technical support to internal operations and data management. Their ability to process and respond to queries in real-time makes them an asset for enhancing productivity and reducing human error.
Benefits of chatbot for manufacturing industry
Enhancing Communication and Collaboration
- Effective communication is crucial in manufacturing environments where timely information exchange can make the difference between seamless operations and costly delays. Chatbots facilitate real-time communication between various departments, ensuring that everyone is on the same page.
- For example, a chatbot can instantly notify the maintenance team of equipment issues reported by production line workers, enabling quick responses and minimizing downtime.
- Additionally, chatbots can serve as intermediaries between suppliers and manufacturers. By providing up-to-date information on inventory levels and order statuses, chatbots help streamline supply chain management, reducing the risk of overstocking or stockouts and optimizing inventory costs.
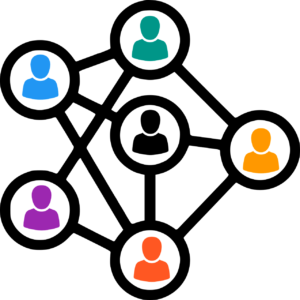
Streamlining Maintenance and Support
- Unplanned downtime is a significant financial drain for manufacturing companies. Chatbots equipped with predictive maintenance capabilities can mitigate this by monitoring equipment health through data from sensors and IoT devices.
- They predict potential failures and schedule maintenance activities proactively, reducing unexpected breakdowns and extending machinery lifespan.
- Additionally, chatbots provide immediate technical support to factory workers. When issues arise, employees can query the chatbot for troubleshooting guidance, enabling quicker resolutions without waiting for a technician. This not only saves time but also ensures continuous production with minimal interruptions.
- By reducing downtime and offering real-time support, chatbots enhance operational efficiency and contribute to substantial cost savings, making them invaluable assets in the manufacturing industry.
Optimizing Workforce Management
- Managing a manufacturing workforce involves complex tasks like scheduling shifts, tracking attendance, and ensuring safety compliance. Chatbots automate these administrative functions, freeing human resources for strategic tasks.
- For instance, chatbots handle shift scheduling by considering employee availability, skill sets, and production demands, ensuring optimal staffing. Additionally, chatbots assist in training new employees by providing instant access to training materials, safety protocols, and operational guidelines.
- This helps new hires quickly acclimate to their roles, enhancing productivity and reducing the time spent on manual training, ultimately optimizing workforce management.
Enhancing Data Management and Decision Making
- Data is a critical asset in modern manufacturing, driving decision-making and operational improvements. Chatbots play a pivotal role by collecting, analyzing, and presenting data in a user-friendly format, enabling managers to make informed decisions swiftly.
- They generate real-time reports on key performance indicators (KPIs) such as production output, quality control metrics, and supply chain performance. This immediate access to crucial data allows managers to identify inefficiencies, predict demand trends, and implement corrective actions promptly.
- By leveraging this comprehensive data, manufacturers can enhance overall operational efficiency, optimize resource allocation, and manage costs more effectively.
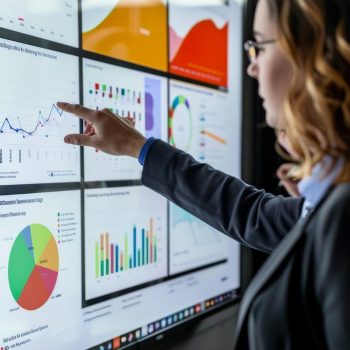
Training and Onboarding
- Chatbots play a crucial role in training new employees by offering instant access to training materials, safety protocols, and operational guidelines. This immediate availability of resources significantly accelerates the onboarding process, enabling new hires to quickly familiarize themselves with their roles and responsibilities.
- With chatbots, new employees can access essential information at any time, eliminating the need to wait for scheduled training sessions. They can query the chatbot for specific instructions or guidelines, ensuring they receive precise and consistent information. This not only speeds up the learning curve but also reduces the likelihood of errors due to miscommunication or misunderstanding.
- Moreover, chatbots can deliver interactive training modules, quizzes, and simulations, making the learning experience more engaging and effective.By providing real-time feedback and support, chatbots help reinforce knowledge and ensure that new employees are well-prepared to perform their duties.
- New hires become productive members of the team more quickly, contributing to the overall efficiency and effectiveness of the manufacturing operation. This streamlined approach to training enhances the workforce’s competency and readiness, ultimately benefiting the entire organization.
Enhanced Customer Experience
- Chatbots significantly enhance the customer experience by efficiently handling inquiries, providing product information, and processing orders. Their ability to operate around the clock ensures that customers receive immediate responses, regardless of the time of day.
- The efficiency of chatbots reduces wait times and minimizes the frustration associated with traditional customer service channels, where customers might be placed on hold or have to navigate complex menus.
- By delivering prompt and effective service, chatbots contribute to a more positive interaction between the customer and the company.This 24/7 availability is crucial in today’s fast-paced world, where customers expect quick and efficient service.
- Furthermore, chatbots can personalize interactions based on customer data, offering tailored recommendations and solutions. This personalization enhances the customer’s experience, making them feel valued and understood.
Real-World Applications and Success Stories
- Several leading manufacturers have successfully integrated chatbots into their operations, realizing significant benefits. For instance, an automotive manufacturer used chatbots to improve supply chain communication, resulting in a 20% reduction in lead times and a 15% decrease in inventory costs.
- Similarly, an electronics company deployed chatbots for predictive maintenance, cutting equipment downtime by 30% and saving millions in repair expenses.
- These success stories highlight the tangible impact of chatbots on manufacturing operations, showcasing their potential to drive efficiency and cost savings.
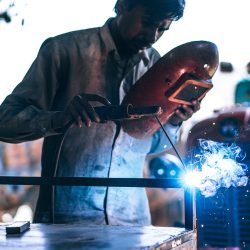
The Economic Impact of Chatbots in Manufacturing
- The economic impact of chatbots in the manufacturing industry is profound. By automating routine tasks, improving communication, and enhancing decision-making, chatbots contribute significantly to cost savings. These savings can be reinvested in further technological advancements, fostering a cycle of continuous improvement and innovation.
- Chatbots streamline operations by handling administrative tasks such as scheduling, inventory management, and real-time communication between departments. This automation reduces the need for manual intervention, minimizing human errors and operational delays.
- Predictive maintenance capabilities of chatbots further enhance efficiency by monitoring equipment health, predicting potential failures, and scheduling maintenance proactively. This minimizes unplanned downtime and extends the lifespan of machinery, translating to substantial cost savings.
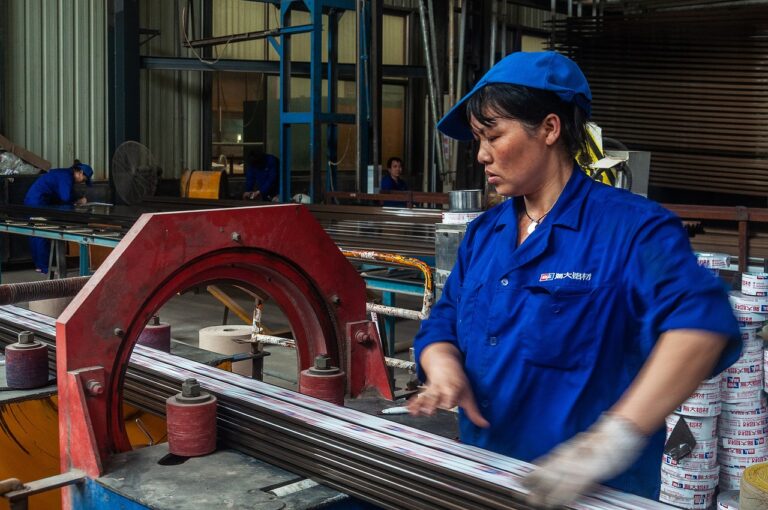
- The data-driven insights provided by chatbots are invaluable for decision-making. By collecting and analyzing real-time data on production metrics, quality control, and supply chain performance, chatbots enable managers to identify inefficiencies and implement corrective actions promptly. This leads to better resource allocation and cost management, further driving economic benefits.
- The efficiency gains achieved through chatbot integration lead to higher productivity and output, boosting the overall profitability of manufacturing operations. Real-world applications demonstrate these benefits, with manufacturers reporting significant reductions in lead times, inventory costs, and equipment downtime after implementing chatbots.
- As the manufacturing industry continues to evolve, the role of chatbots in driving economic success will become increasingly prominent. Their ability to streamline operations, enhance decision-making, and optimize resources makes them indispensable tools in the quest for efficiency and cost-effectiveness, shaping the future of manufacturing.
Conclusion
Chatbots are revolutionizing the manufacturing industry by enhancing communication, streamlining maintenance, optimizing workforce management, and improving data-driven decision-making. Their ability to automate routine tasks and provide real-time insights is transforming factories into more efficient, cost-effective, and innovative environments. As manufacturers continue to embrace digital transformation, the adoption of chatbots will undoubtedly play a crucial role in shaping the future of the industry.